Independent Performance Reports
Performance Reports for Your Cathode Materials
The development and characterization of battery materials is a key process for improving the performance and service life of modern energy storage systems. To evaluate the quality and efficiency of new battery materials, we offer you a comprehensive catalog of services covering various phases of material development and characterization. This includes the development of slurries (electrode pastes), the coating of electrode foils, the electrochemical characterization of electrodes and a complete investigation of the electrochemical performance of prototype cells. Contact our team for an independent performance report for your battery materials.
Development of the Electrode Pastes (Slurry)
The production of a homogeneous and stable slurry is a critical parameter of high-quality battery materials. The slurry development process involves several steps.
Material selection: Selection of suitable active materials (e.g. lithium iron phosphate (LFP), NCM, or other materials), conductive additives (e.g. carbon black, graphene) and binders (e.g. polyvinylidene fluoride (PVDF), water-based systems).
Optimization of the mixing ratios: Defining the optimal composition, including active material, conductive additive and binder. This is crucial to maximize the conductivity, stability and adhesion of the electrodes.
Solvent and viscosity: Adjustment of the solvent system (e.g. N-methyl-2-pyrrolidone (NMP) or water-based systems) and the viscosity of the slurry to ensure a uniform coating.
Mixing method: Use of appropriate mixing methods (e.g. planetary mixers, high speed mixers) to ensure a homogeneous slurry with the correct particle distribution.
Controlled particle size distribution: Optimization of the particle size distribution of the active material to improve electrode performance and increase cyclization stability.
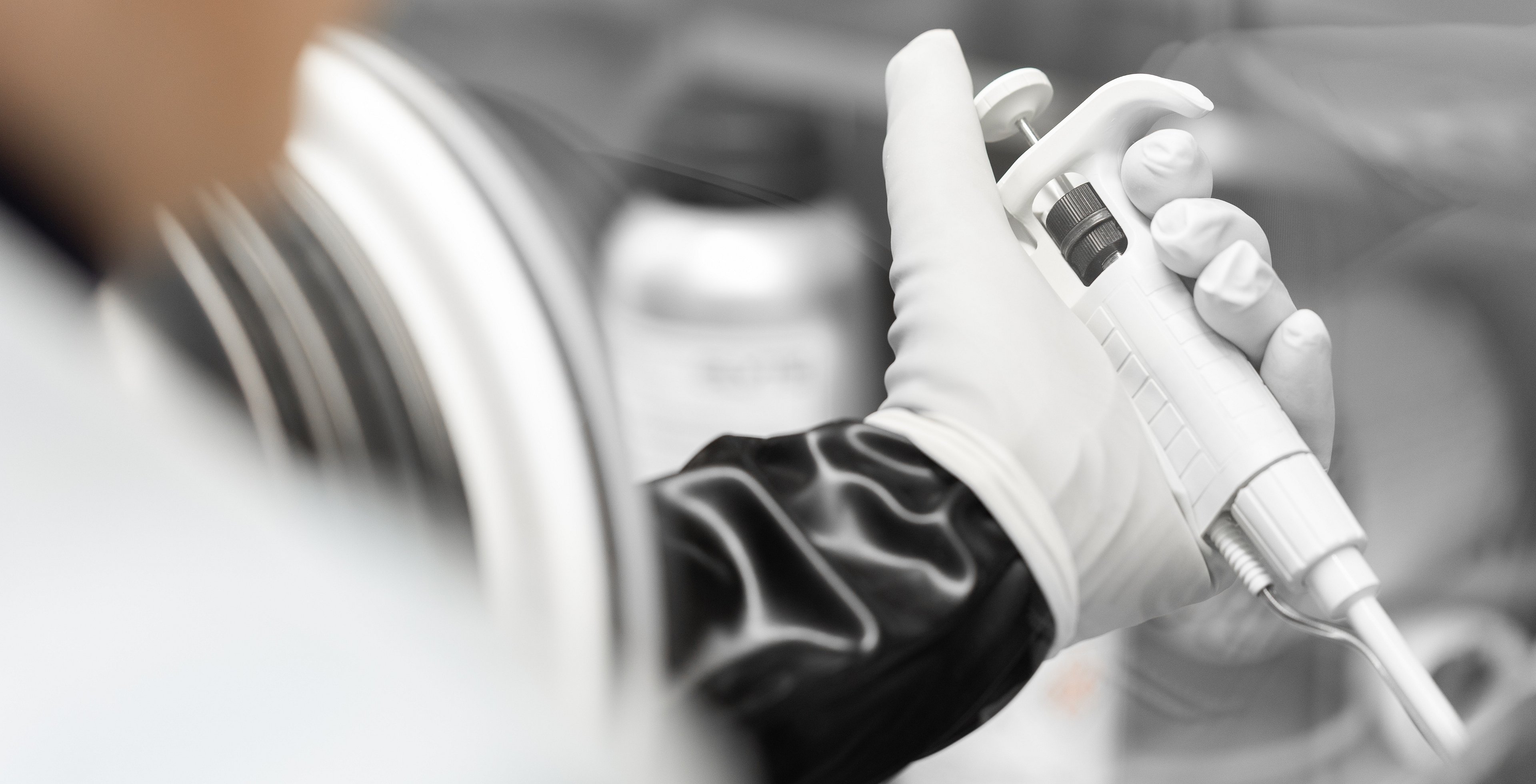
Coating Process of the Electrodes
Once the slurry is prepared, the coating process follows, in which the material is applied evenly to the current-carrying substrates (e.g. aluminum for cathodes and copper for anodes).
Coating method: Selection and application of a suitable coating method, such as doctor blade coating or slot die coating, to ensure a uniform coating thickness of the electrode.
Adjusting the layer thickness: The layer thickness of the coating is optimized depending on the cell capacity and material requirements. This has a significant influence on the energy density and internal resistance of the cell.
Drying: Optimization of the drying process to ensure that the solvent is completely removed and the electrodes have a stable structure. The drying temperature and duration are crucial here.
Calendering: Calendering of the coated electrode film (compacting) to optimize the particle structure and achieve high energy density and good mechanical stability.

Electrode Characterization
After coating and drying, the electrodes must be characterized for their structural and chemical properties to ensure that they meet the requirements.
Thickness and weight: Precise measurements of the thickness and weight of the electrodes to ensure uniform mass loading and to be able to calculate the cell capacity accurately.
Porosity and density: Analysis of the porosity and density of the electrodes. Optimal porosity is critical for electrolyte diffusion and cell performance.
Adhesion test: The adhesion of the coating to the substrate is checked to ensure that the electrodes remain stable under mechanical stress.
Microscopic examinations: Using scanning electron microscopy (SEM) and other techniques, the morphology of the electrodes is examined to confirm homogeneous distribution of the active material and good bonding between the particles.
Chemical analysis: Analyses such as X-ray diffraction (XRD) and Raman spectroscopy are carried out to confirm the crystalline structure and chemical composition of the material.
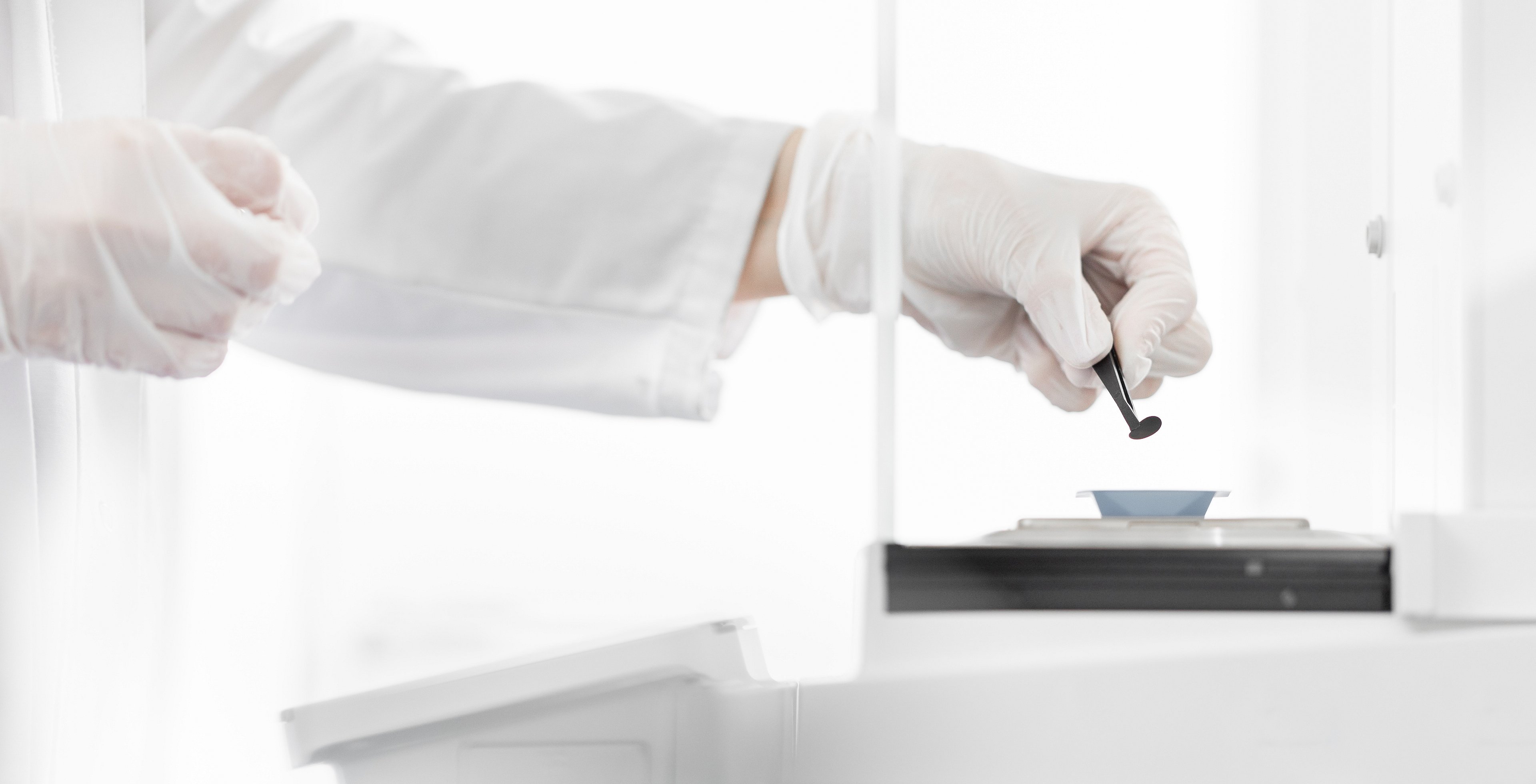
Electrochemical Tests
Electrochemical characterization is the final step in evaluating the performance of the electrodes and prototype cells produced.
Cell assembly: The electrodes are mounted in button cells or pouch cells in order to carry out standardized electrochemical tests. Suitable electrolytes and separators are used that meet the requirements of the materials.
Capacity tests: Cyclic charge and discharge tests at different C rates (discharge currents) are carried out to determine the specific capacity of the materials. The cell is tested over several cycles to determine its longevity and cyclization stability.
Rate tests: To test the performance of the cell under different loads, rate tests are carried out in which the cell is charged and discharged at different current rates (e.g. C/10 to 5C). These tests show the kinetic properties of the materials.
Impedance spectroscopy (EIS): Electrochemical impedance spectroscopy is used to determine the internal resistance of the cell and to obtain information about the charge transfer resistance and diffusion properties.
Cycle life: Long-term cycling is performed to evaluate the degradation of the materials over many charge and discharge cycles. These tests are crucial to estimate the lifetime of the cell in real applications.
Temperature tests: Electrochemical tests at different temperatures (e.g. 0°C, room temperature, 60°C) are carried out to evaluate the performance of the materials under extreme conditions.
Results Analysis and Report Preparation
Once the investigation is completed, the results are analyzed and summarized in a detailed report. This report contains all the key points that you can use in your own work.
Summary of material properties, including mechanical and structural analysis of the electrodes.
Electrochemical results, such as specific capacity, cycle life and rate tests.
Optimization suggestions to improve material properties and electrochemical performance.