Electrode Coating
Coating of Anode and Cathode Materials
IBUvolt develops solutions to coat anode or cathode materials according to your specific requirements. Our experienced team will work closely with you to ensure that the electrodes meet your exact requirements. We support you in achieving optimal results for your research and development. Whether it's specific material combinations or special coating thicknesses, we flexibly adapt our coating processes to your needs. Let us know your requirements and we will develop an individual solution for you that is perfectly tailored to your projects.
The development of formulations for electrode slurries requires a systematic approach, starting with the selection of suitable active materials, binders and solvents. Target parameters such as electrode loading, density and stability are then defined and the formulation is optimized by adjusting the ratio of components and viscosity.
The mixing process then takes place in several stages to ensure a homogeneous slurry. The slurry is then applied to the current collector and dried, followed by compaction by calendering. Finally, the finished electrode is characterized and tested for long-term stability and electrochemical performance. The process must aim to achieve the specified parameters of loading, density and stability of the coated electrodes.
Electrode Coating – the Process
For the successful coating of electrodes in the laboratory, careful optimization and checking of the individual work steps is essential in order to achieve the desired properties of the electrodes and at the same time obtain reproducible results.
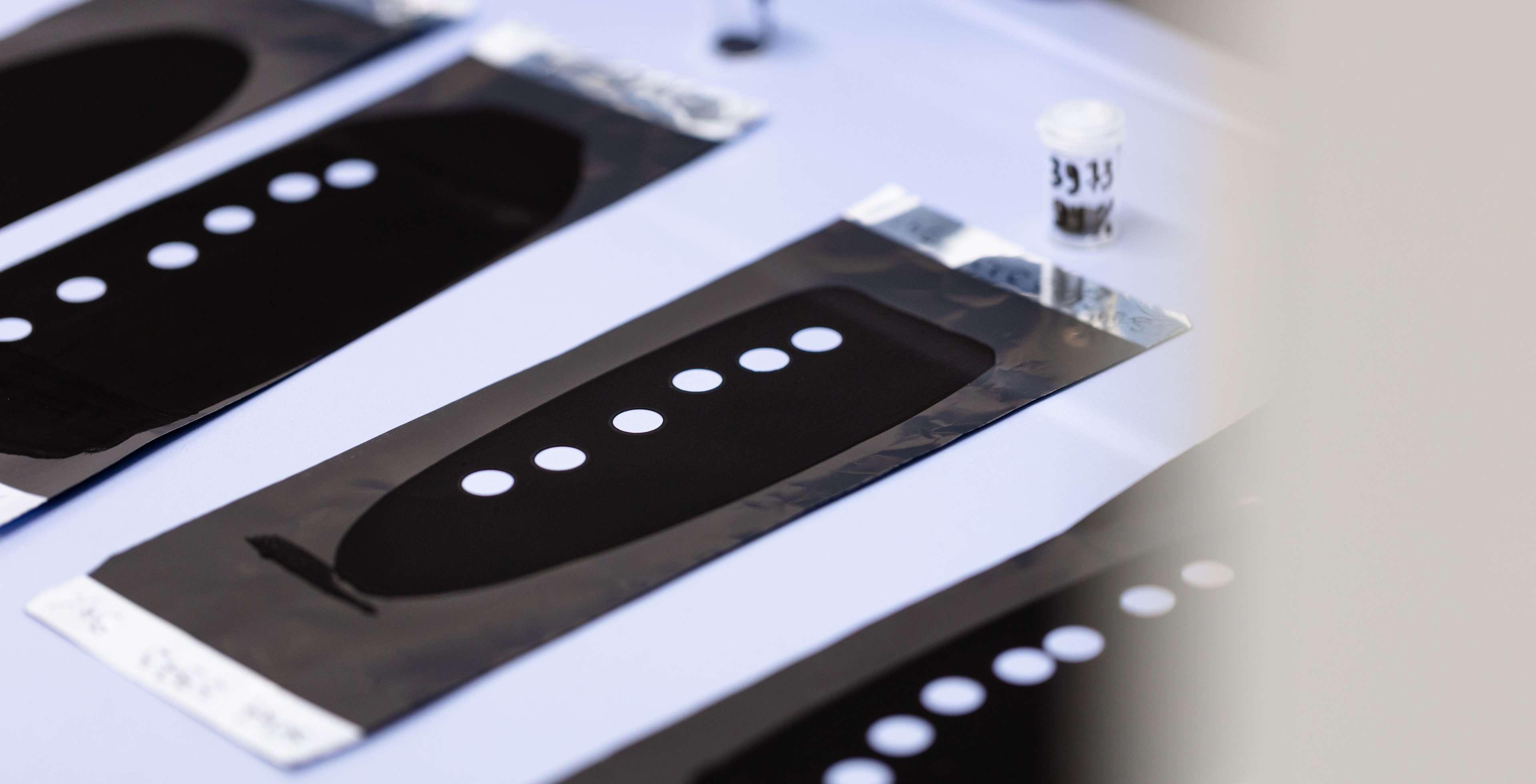
Material Selection for Electrode Coating
Active materials: We process your materials according to your wishes!
Conductive additives: Addition of conductive additives such as carbon black or carbon nanotubes to improve electrical conductivity.
Binder: Selection of a suitable binder (e.g. polyvinylidene fluoride (PVDF) or carboxymethyl cellulose (CMC)) for the mechanical stability of the electrode.
Solvent: The choice of a suitable solvent (e.g. N-methyl-2-pyrrolidone (NMP) or water, depending on the binder) to dissolve the binder and homogenize the slurry.
Determination of the Target Parameters
Electrode loading: Determination of the target loading (active material per unit area) of the electrode required for the desired energy density.
Electrode density: Target specification of the density of the electrode after drying and compaction in order to achieve a good volume and energy density.
Stability: Ensuring that the slurry is stable, i.e. that no sedimentation or segregation occurs during processing.
Optimization of the Slurry Recipe
Ratio of components: Determining the ratio of active material, lead additive, binder and solvent. These ratios influence the rheology, loading and density of the final electrode.
Rheology adjustment: The viscosity of the slurry must be optimized for the coating process. Too liquid leads to uneven coating, too viscous makes application more difficult.
Mixing Process
Premixing: All components (active material, conductive additives, binder and solvent) are premixed in a defined sequence and speed.
Dispersing: The homogeneity of the slurry is crucial. High energy mixing techniques such as ball mills or ultrasonics can be used to break agglomerates and ensure uniform distribution of particles.
Mixing time and speed: These parameters must be adjusted so that the slurry remains homogeneous but is not overmixed, which could lead to undesirable effects such as destruction of the binder.
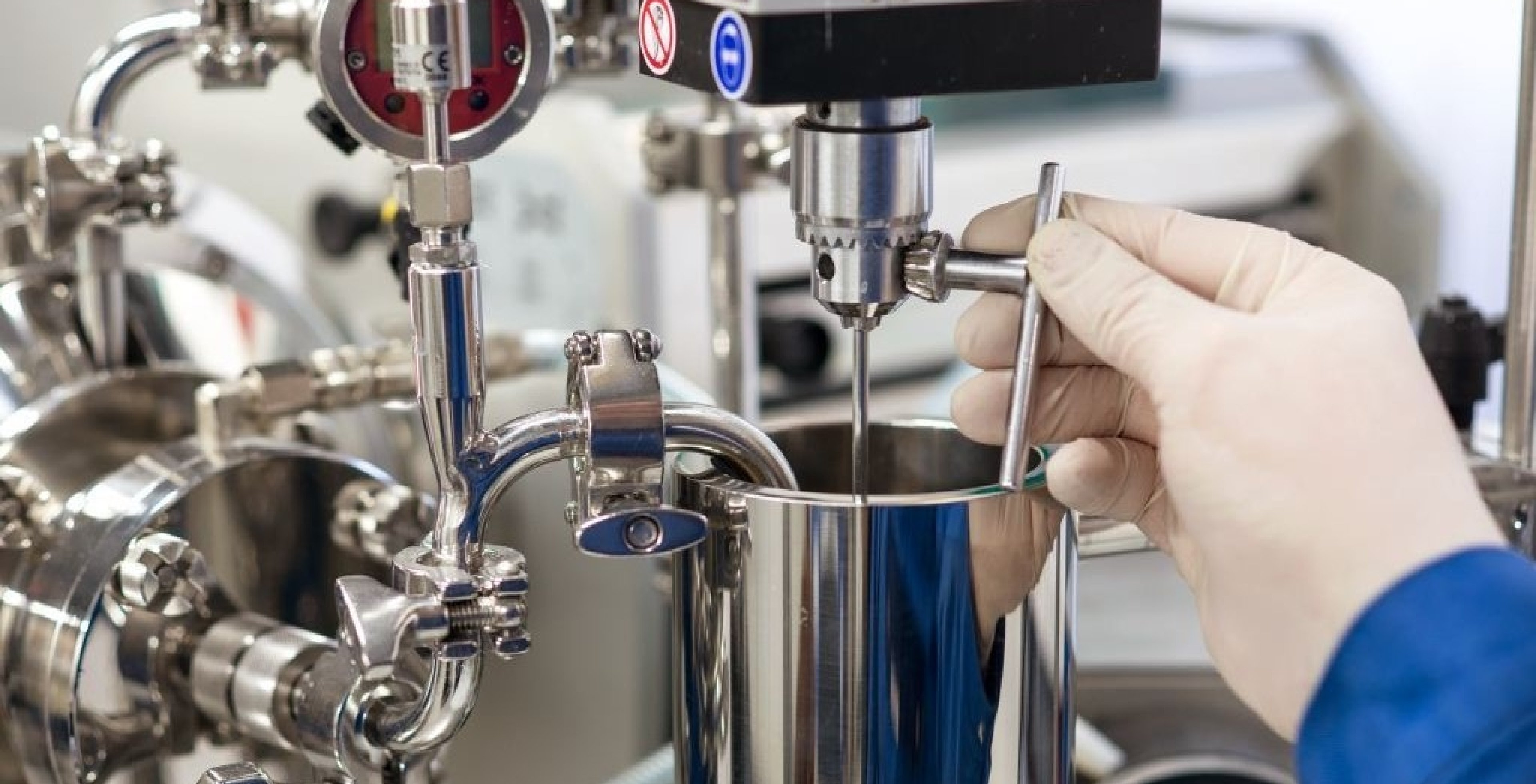
Coating Process
Application of the slurry: The slurry is applied to the current collector (e.g. copper foil or aluminum foil), usually by a doctor blade or slot die coating process.
Coating thickness control: The thickness of the wet coating largely determines the subsequent electrode loading and must be precisely controlled.
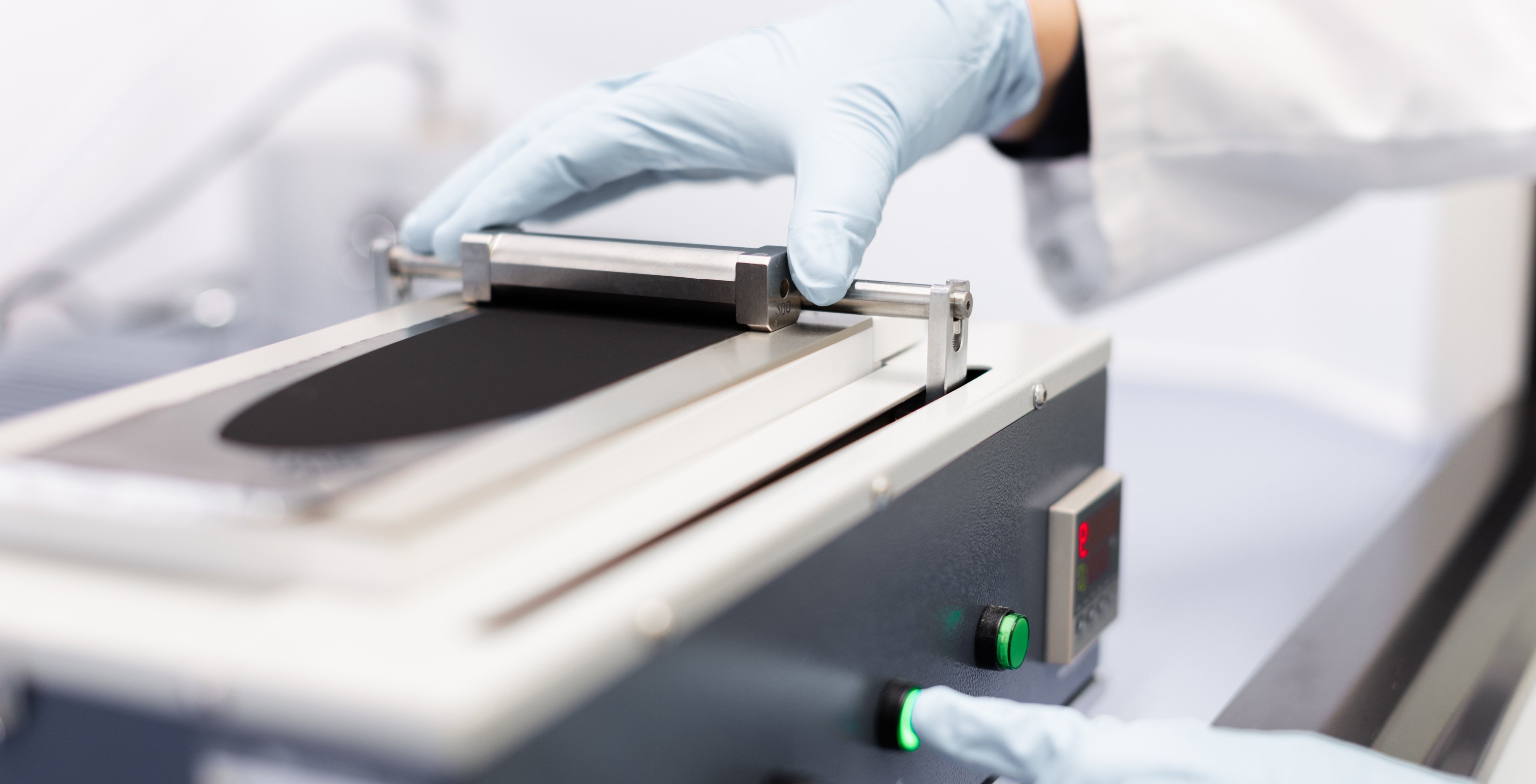
Drying
Drying temperature and time: The solvent must evaporate after coating. Drying too quickly can cause cracks, while drying too slowly can lead to agglomerates or uneven layer formation.
Solvent removal: Depending on the slurry composition, the solvent must be completely removed to ensure a stable electrode.
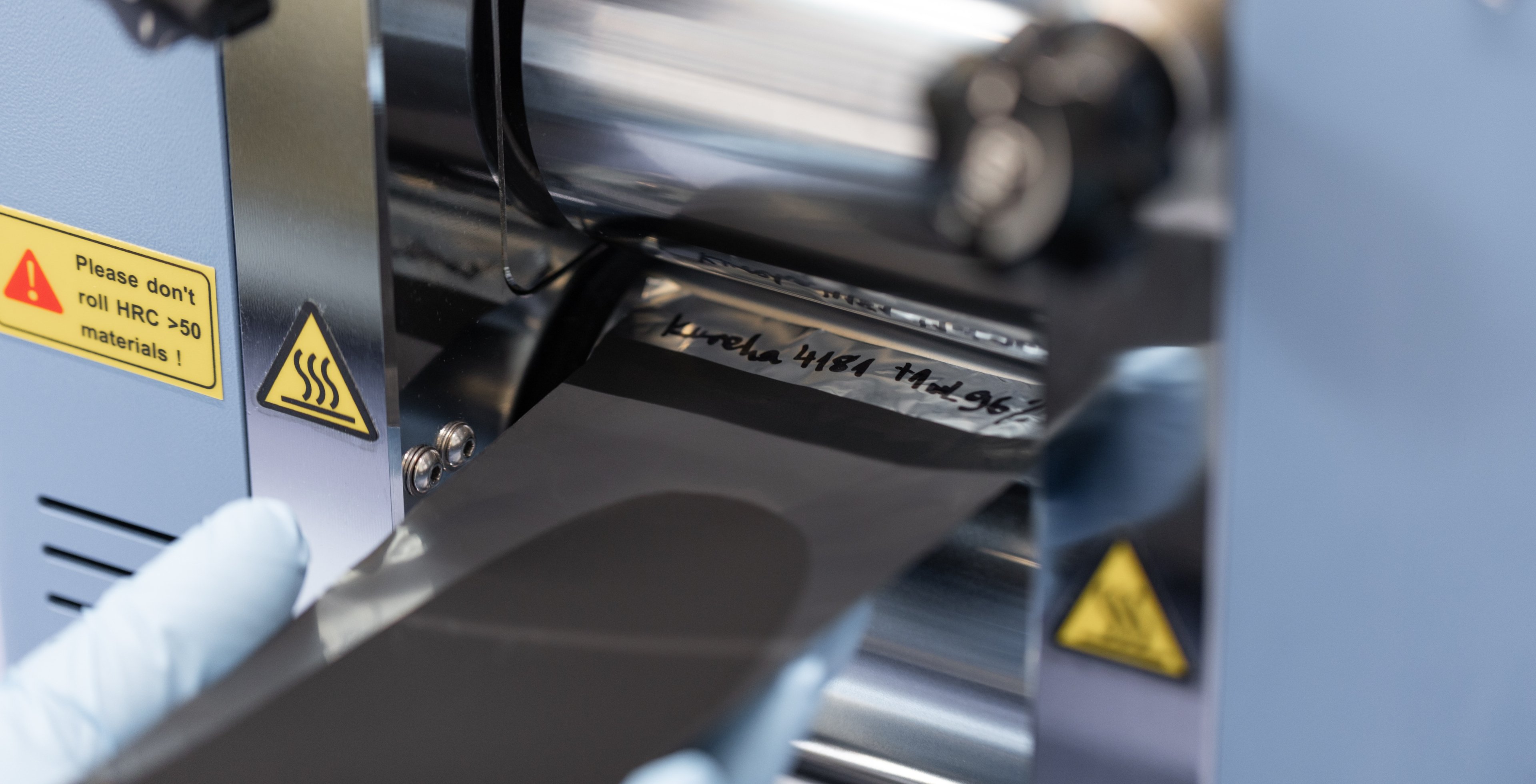
Compaction (Calendering)
After drying, the electrode is compacted by a calendering process (roller press) to increase the density and improve the contact between the particles.
Calendering parameters: The roller pressure force and temperature must be optimized to achieve the desired density and porosity without compromising the mechanical integrity of the electrode.
Characterization
Coating thickness and loading: Determination of the coating thickness and specific loading of the electrode after coating and compaction.
Porosity: Measurement of porosity to ensure that the electrode has the necessary ion permeability and a good balance between density and performance.
Electrode adhesion: Testing the mechanical stability of the electrode on the current collector (adhesion tests).
Stability Test
Long-term stability of the slurry: Check whether the slurry remains stable over a longer period of time (no segregation or sedimentation).
Electrochemical performance testing: Testing the performance of the coated electrode in a test cell to ensure that the cycle stability, energy density and capacity meet the requirements.