Electrochemical Analyses
State-of-the-Art Laboratory for the Determination of Electrochemical Properties
Use our electrochemical laboratory for analyses and your research on battery materials! Since 2021, IBUvolt operates an electrochemical laboratory for the development and quality control of our cathode materials IBUvolt® LFP and IBUvolt® NMO. We maintain facilities for battery testing and for investigating electrochemical processes in the battery: measuring voltages, currents and electrical resistances as well as carrying out potentiostat and galvanostat measurements. Use our service to evaluate measurement results and analyze them using artificial intelligence.
Determination of Electrochemical Properties
Our E-chemistry laboratory in Weimar covers all battery material research methods: from chemical-physical analysis and electrode technology to cell preparation and defined charging and discharging under climate-controlled conditions. The focus is on understanding and controlling the electrochemical processes on the electrode surfaces and in the volume of the active layer.
The quality and performance of the tested battery active materials are determined in order to determine the performance parameters of the material from our production and to be able to take the findings into account in further development steps.
Dr. Katja Kretschmer and her team will be happy to support you with your analytical questions! Head of Laboratory Analysis, Chemist, Technische Universität Carolo-Wilhelmina zu Braunschweig & University of Technology, Sydney, 10 years of professional experience as a researcher in chemical engineering, materials science and electrochemistry.
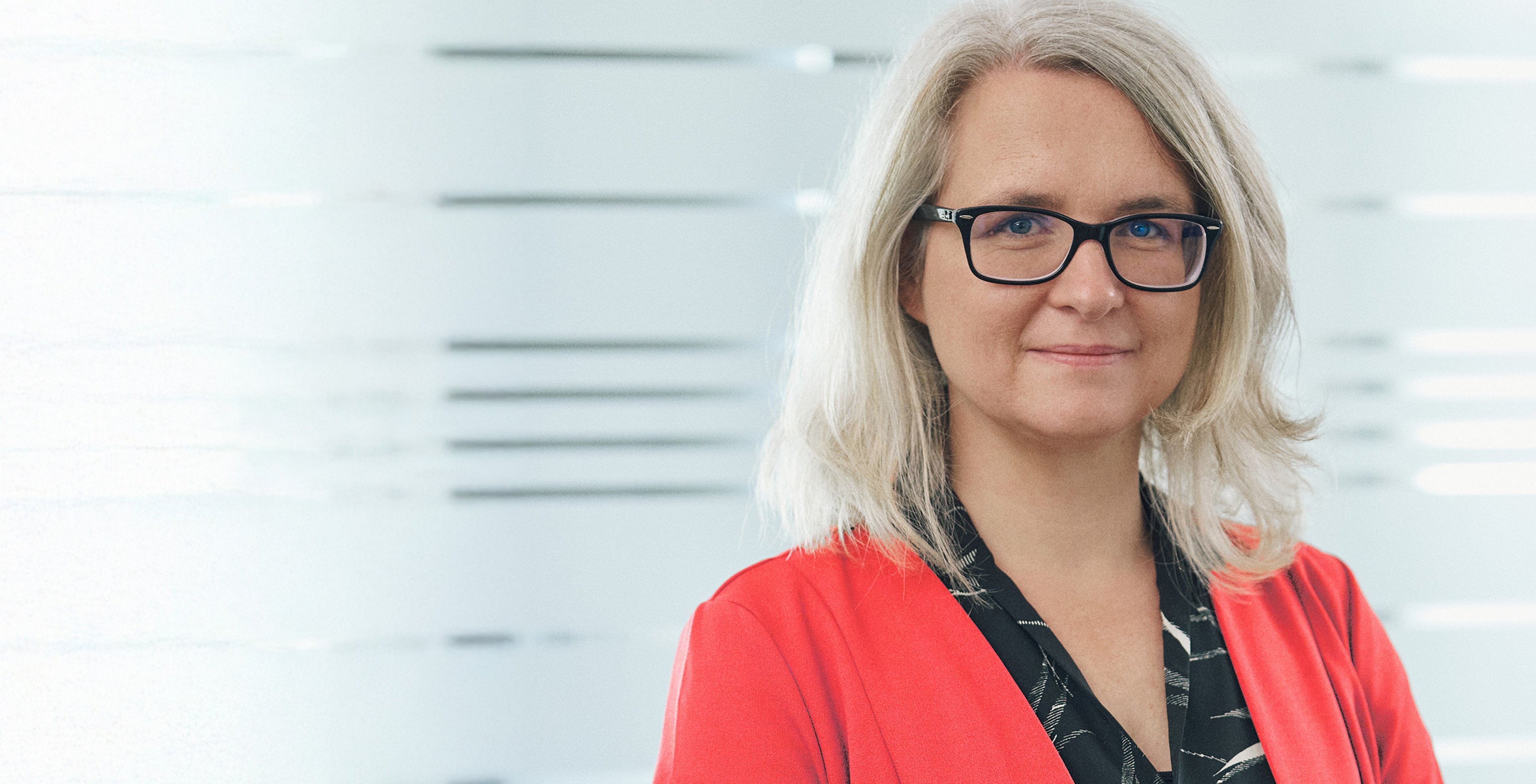
Active Powder to Battery Testing in the Laboratory
The entire process from powder material to cell preparation is covered with modern equipment for the electrochemical testing of battery materials in button cells (CR2016, CR2025 and CR2032) and Swagelok cells.
The electrode slurry must be prepared under a controlled atmosphere, applied with micrometer precision and the electrode is then calendered, whereby temperatures of up to 100 °C can be employed in a controllable manner. The punch-pressed electrodes are then deep-dried at up to 300 °C under vacuum atmposphere and transferred to a glovebox under an argon atmosphere, where the battery cell manufacturing takes place at a controlled oxygen content and humidity.
To characterize the cell composition and for material tests, we maintain equipment in the power range of up to ±5A and ±10V. In addition to capacitive voltage measurements, we are also able to implement various pulse methods and switch between potentiostatic and galvanostatic modes in less than 10μs, even for sophisticated characterization methods such as electrochemical impedance spectroscopy.
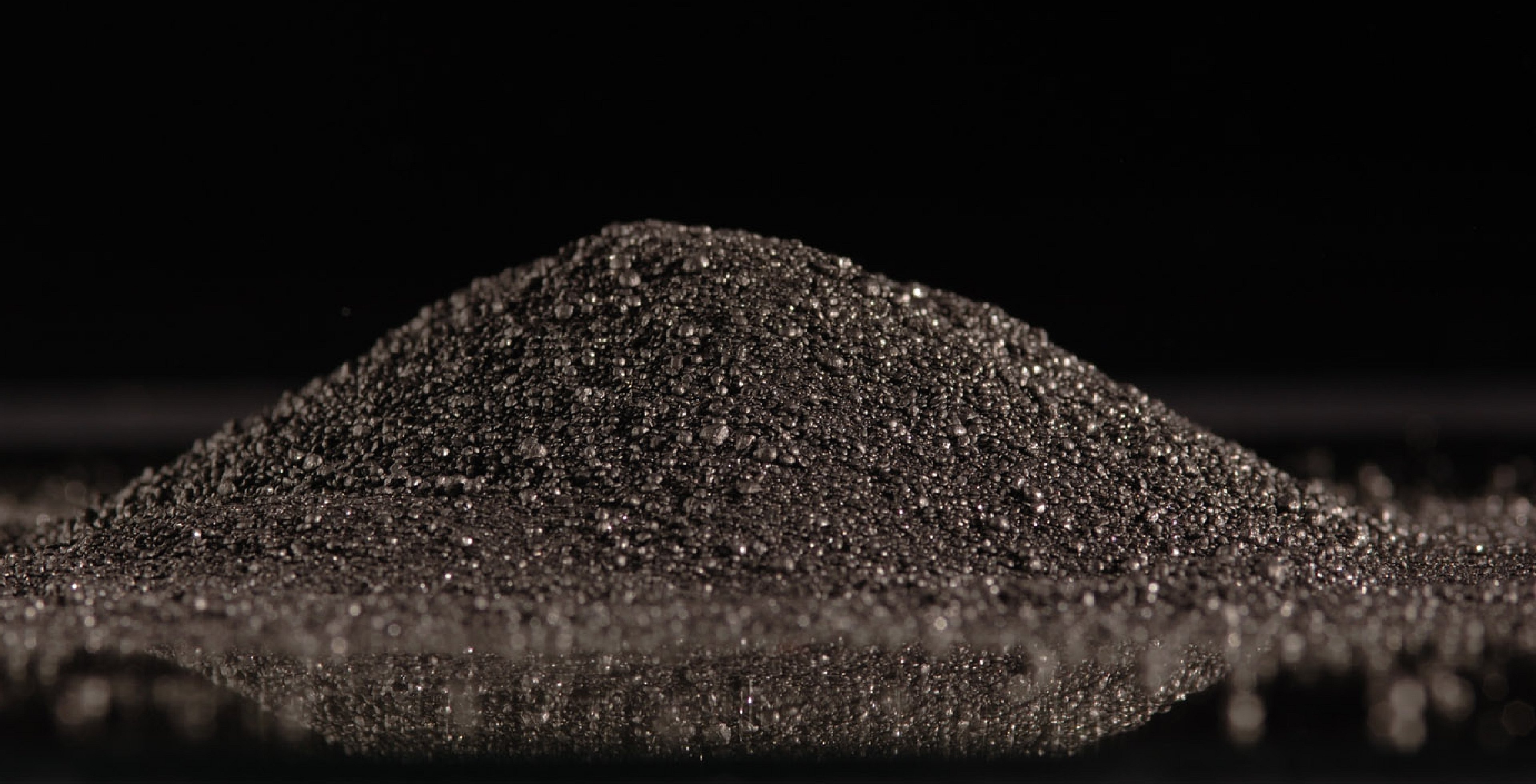
Equipment in our E-Chemistry Laboratory
- From slurry to finished battery cell
- Centrifugal mixer
- Slurry coating applicator with heating function
- Vacuum furnace with heating option
- Cutting press
- Precision scale
- Calender with heating function
- Hydraulic crimper with set for post-mortem analysis
- SP glovebox with gas cleaning and controlled atmosphere
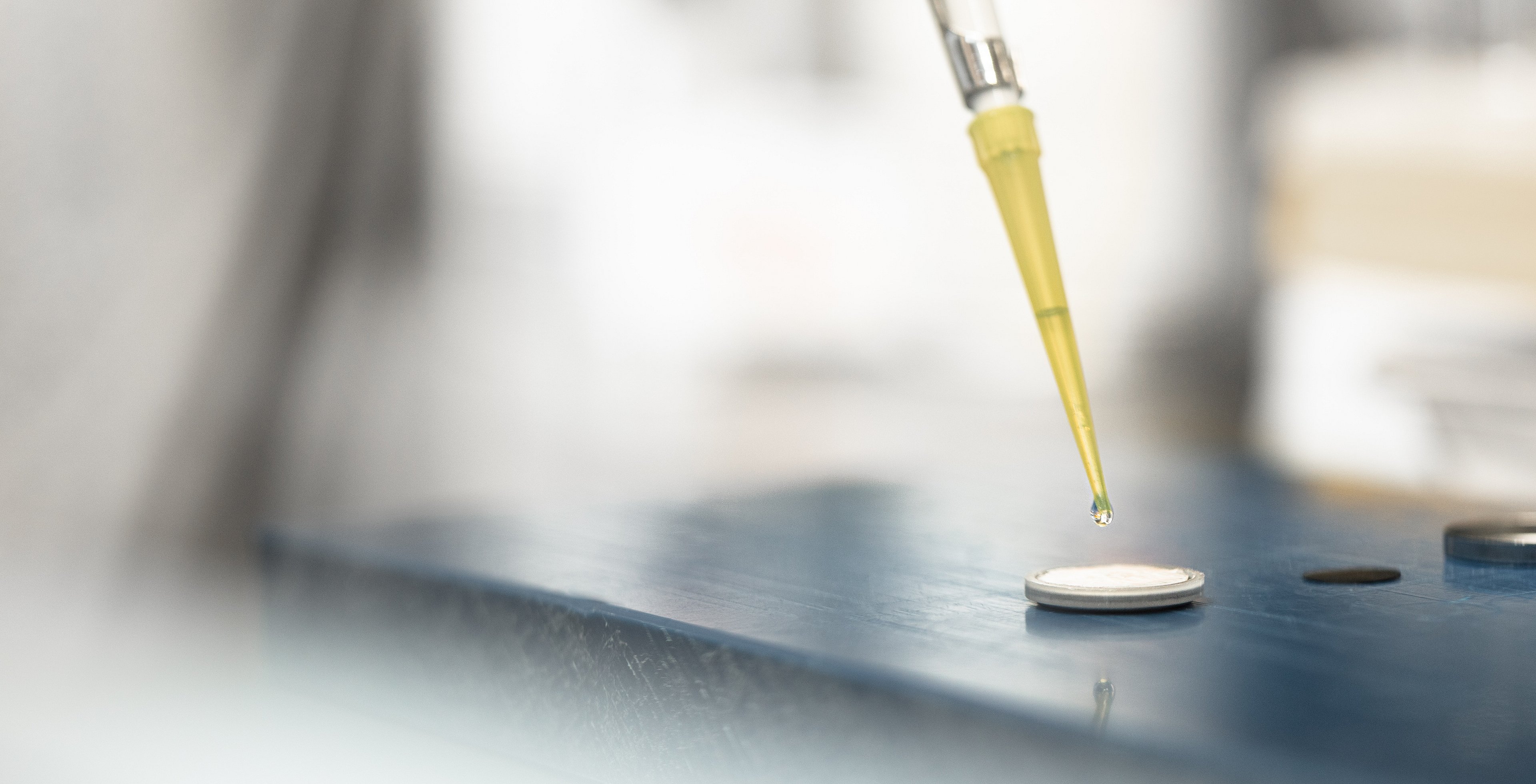
Steps of Electrochemical Analyses at IBUvolt
Get to know our approach and the eye for detail with which we also analyze your materials!
Cell Assembly
The button cell is assembled in an oxygen-free environment (e.g. in a glove box with argon or nitrogen). The LFP cathode is applied to an aluminum foil and used as an electrode in the cell. The lithium metal anode is placed on a copper foil with the separator in between, which is impregnated with the liquid electrolyte to enable ion conduction.
Initial Formation
After assembly, the cells are charged at a constant current charge at a low rate (e.g. C/10, i.e. 10 hours for a full charge) to ensure the formation of the cell components. This is done to activate the full capacity of the cell.
Carry out a Rate Test
A rate test evaluates the battery cell at different discharge rates, typically C/10, C/5, C/2, 1C, 2C, etc. For each rate, the cell is fully charged and then discharged to the final discharge voltage (normally approx. 2.5 V for LFP cathodes). Between rates, the cell is returned to its original capacity to ensure consistent measurements.
Data Recording
The capacitance and voltage are continuously recorded. Typically, it is observed that the capacitance decreases at higher discharge rates, indicating kinetic limitations of the cell.
Analyzing the Results
We plot the capacity as a function of discharge rate. This curve shows how well the cell can handle high currents, indicating the performance of the LFP cathode and the Li-metal anode.