Battery Recycling
Expertise and Capacities in Thermal Process Engineering for your Battery Recycling
The expansion of renewable energies will require considerable amounts of energy storage capacity, which is the focus of current battery development and use. In the foreseeable future, however, this will result in large quantities of “used” batteries – a massive problem for economic efficiency and environmental protection and a challenge for the required process engineering solutions.
The recycling process of such complex material systems often involves a thermal process step – this is where we can help with our many years of experience in the thermal treatment of complex material mixtures! We will support you in process development, into which we can incorporate our wealth of experience in scale-up and plant planning.
EU Requirements for the Recycling of Battery Materials
The EU now stipulates certain requirements and guidelines for the recycling rate in batteries: The recycling rate for lithium is to increase from 50% to 80% between 2028 and 2032. The target for more critical elements such as nickel, copper, cobalt and lead is 90%. The specified proportion of recycled materials in new batteries is also to be set at an increasing level:
Lithium: from 18th of August 2031: 6 % from 18th of August 2036: 12 %
Cobalt: from 18th of August 2031: 16 % from 18th of August 2036: 26 %
Nickel: from 18th of August 2031: 6 % from 18th of August 2036: 15 %
The higher the demands on the recycling of battery materials, the higher the demands on the thermal processes required for recycling – In terms of development and process control. With our many years of experience in thermal process engineering, we can help to develop the required processes and scale them up to an industrial scale.
Recycling Black Mass with Thermal Processes
At the beginning of the recycling process, the batteries must be sorted according to the cathode materials used and discharged. The batteries prepared in this way are mechanically separated into their components as far as possible – by dismantling or complete shredding. After sorting out the coarse components (plastic casings, etc.), what remains of the batteries is a complex mixture of materials – the so-called black mass. The name derives from the large quantities of carbon (graphite) it contains, which gives its eponymous black color. This black mass contains a proportion of valuable materials, such as various metals (e.g. nickel and cobalt), the recovery of which is essential in terms of sustainable materials management. At the same time, black mass is declared as waste material and poses a high environmental risk due to its components (caused by the content of heavy metals and halogenated organic components). A recycling process therefore places difficult demands on the environmental compatibility of the resulting products and the process itself.
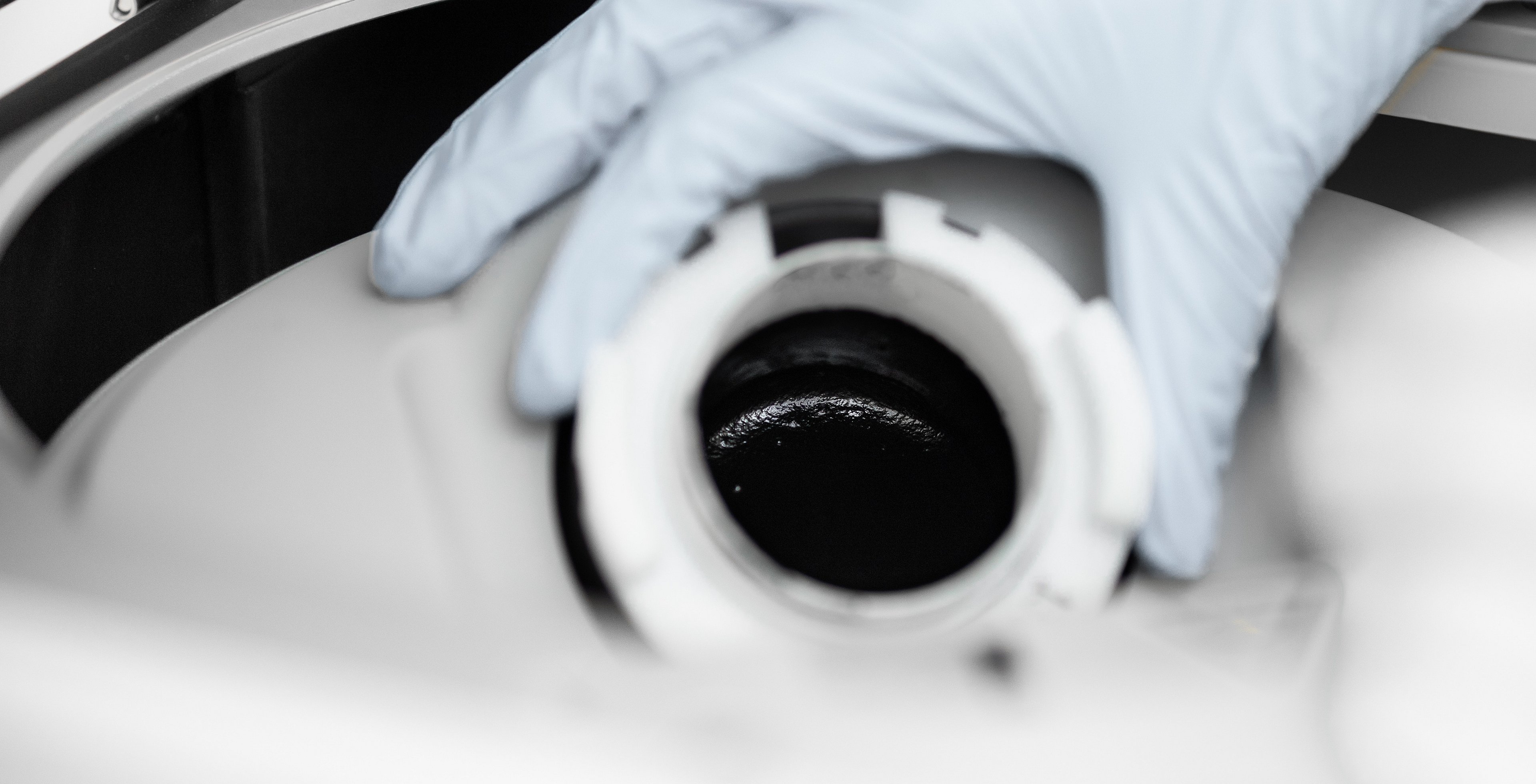
Difficulties in the Treatment of Black Mass
To recover the black mass, used up batteries must first be mechanically treated after the discharge process. Pyrometallurgy is an industrially used process for the resulting black mass. In this process, the black mass is thermally treated. Thermal treatment with the aim of removing organic components and reducing the carbon content can be carried out in a rotary kiln. These steps can be realized at “lower” temperatures of 400 °C to 800 °C. The complexities of these treatment steps lie, among other things, in the waste gas treatment due to the high levels of carbon monoxide or unburned hydrocarbons. Owing to the thermal treatment and the associated decomposition of the conductive salt, hydrogen fluoride can be a component of the exhaust gas, which requires complex and costly exhaust gas purification.
Both the removal of organic components and the reduction of the carbon content in the black mass are important thermal preparation steps in order to achieve a melting phase that is as pure as possible, so that the recovery of valuable materials in the subsequent melting step can be as efficient as possible. These usually take place in other types of furnaces, such as an electric arc furnace, which enables a more efficient treatment of the material a purer molten phase. In addition to this, a slag phase is formed during the melting process and metals like lithium and aluminum are enriched. Processing this phase is more difficult than the melting phase.
How can we Help you with the Treatment of Black Mass?
Having decades of expertise in the thermal treatment of complex material systems, which you can use for process development or scale-up. Our portfolio with rotary kilns of various sizes is available to you for your thermal process steps: from small trials on a laboratory scale to large-scale trials for hundreds of kilograms. Our systems can be used to investigate various treatment conditions such as temperature, treatment duration and reaction atmosphere.
As part of an engineering study program, we will be able to support you in process development for the recycling of battery materials all the way to the planning of a large-scale plant! Starting with the treatment of black mass, we then carry out independent laboratory-scale trials, which we scale up step by step to large-scale production. Based on the data obtained and our expertise, we can design a large-scale plant according to your requirements and provide you with further important information for subsequent processes.