ProLit – Dry Coating of Cathodes
Research Project for the Development of Lithium-Ion Battery Cathodes for Large-Scale Dry Coating
Today's batteries and super capacitors are filled with electrodes (anodes and cathodes), which are usually processed using wet chemistry. This means that a paste dispersed in an organic solvent must be applied to the current collector during the manufacture of the electrodes and then dried. The industry adopted drying is a long and energy-intensive process, while also requiring equipment to remove toxic solvents from the exhaust air for compliance with environmental regulations.
Dry-Coating of Cathodes
Dry coating is a new manufacturing process based on a dry film that makes the use of toxic solvents superfluous. From an ecological point of view, the elimination of solvents promises high energy efficiency through lower energy consumption in the optimized process and shorter process times. In general, dry coating can increase the CO2 balance and the economic efficiency of battery cell production.
Focus of the ProLiT project is thus the dry coating of cathodes (for lithium-ion batteries, LIB). The project is part of a funding initiative of the Federal Ministry of Education and Research (BMBF) and was started 3 years ago (January 1, 2022).
ProLiT combines the development of LIB materials (cathode and binder materials) with process and systems development targeting a scalable and competitive process. Production of a dry powder mixture of the corresponding active material, conductive additive and a thermoplastic binder is essential for dry coating! The decisive factor here is the homogeneous distribution of the components, which means that the mixtures can be processed into a stable electrode with a binder content of five percent or less. In a further process step, this powder mixture is then transferred to the aluminum foil on the cathode side and then permanently affixed by thermomechanical treatment with a roller calendar. The mechanically stable electrodes are then assembled into test cells (button or pouch cells) and characterized electrochemically.
IBUvolt Expertise
With our expertise in thermal process engineering, producing lithium iron phosphate (LFP) cathode materials, we are positioned at the beginning of the development chain. The aim is to adapt and optimize LPF materials for the dry coating process in order to achieve the required electrode properties (good adhesion, density, porosity, conductivity): a material that mixes well with the conductive additive, does not cause agglomerates and subsequently enables good fibrillation.
Our commercially available IBUvolt® LFP400 and some R&D grades have already been tested to meet the project requirements. IBUvolt® LFP400 turned out to be a very good candidate for dry coating. In addition, certain R&D grades showed good processability, effortless aluminum foil coating and good capacity.
Another unique characteristic of the project is the systematic development of a performance-efficient industrial process in conjunction with product development. This involves the consideration of scalable mixing processes for achieving certain structures in the material using a batch mixer and a continuous process in the extruder, continuous dosing of the powder and a multi-stage coating process.
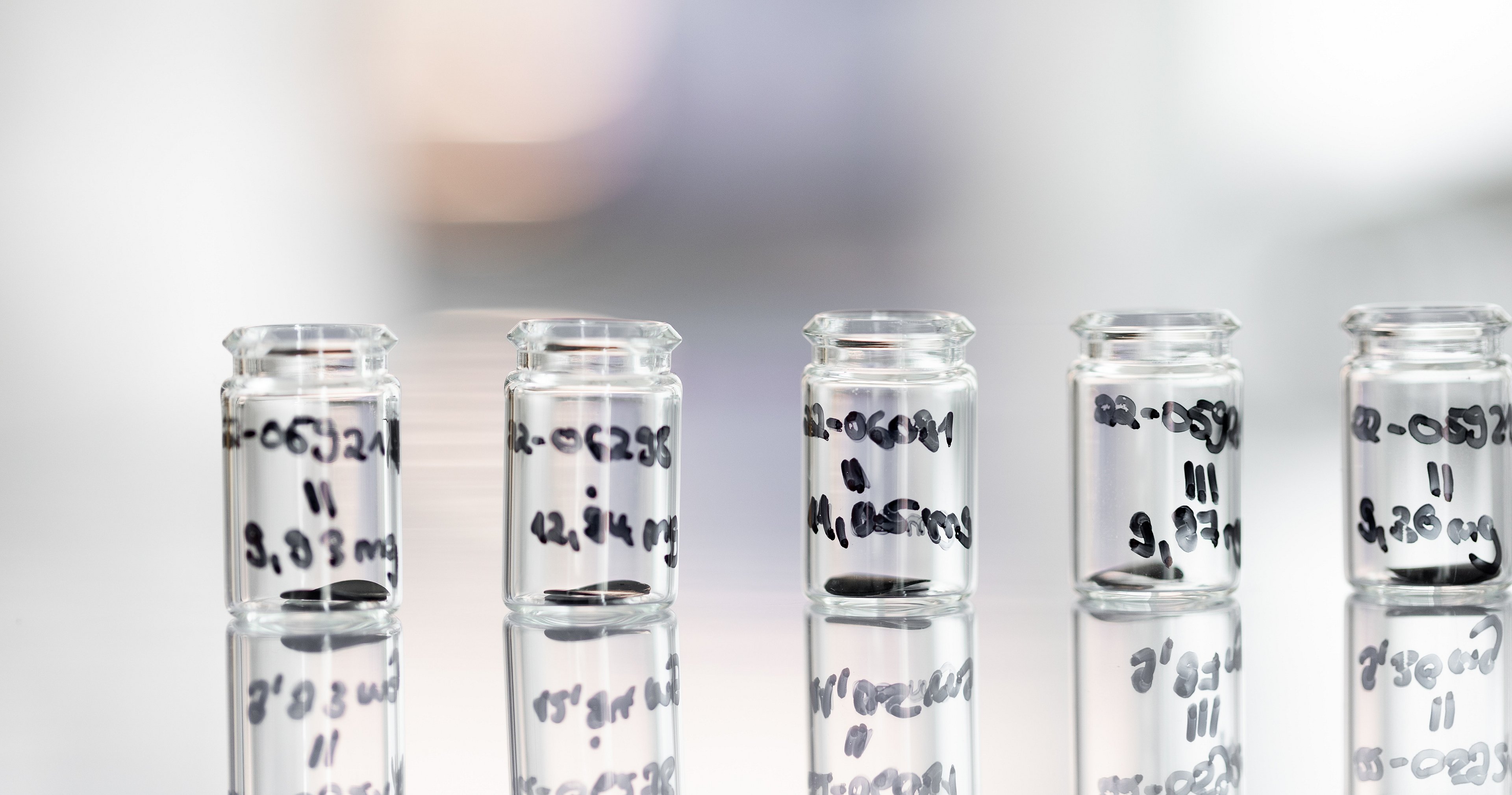
The ProLit Project Consortium
Our project partners are made up of material manufacturers, machine and plant manufacturers, cell manufacturers and scientists from the German industrial and research landscape: Customcells Holding GmbH, Daikin Chemical Europe GmbH (manufacturer of the binding materials), Matthews International GmbH Department Saueressig Engineering, Institute for Particle Technology/ BLB of the TU Braunschweig and MEET Battery Research Center of the Westfälische Wilhelms-Universität Münster (WWU). Further associated partners include Coperion K-tron Deutschland GmbH, Maschinenfabrik Gustav Eirich GmbH & Co. KG, Umicore N.V (produces the Ni-rich nickel-manganese-cobalt material, NMC) and BMW AG.