ENTISE - Development of a Sodium-Ion Battery
Research on a New Environmentally Friendly and Cost-Effective Sodium-Ion Battery!
Resources are limited and today's battery materials are criticized for being dangerous. Against this backdrop, how interesting the idea of being able to produce energy storage devices from non-hazardous and widely available materials sounds! We are researching this possibility together with partners in the “Entise” project. The BMBF research project was launched with the aim of developing a high-performance, cost-effective and environmentally friendly cell chemistry for sodium-ion batteries and converting it into industrially usable cell formats.
Sodium-ion batteries are promising for a sustainable and resource-saving future of energy storage. Sodium is not only inexpensive and abundant, but also safe and easy to recycle. The challenge is to transfer this technology into industrially usable and scalable cells. This is where the ENTISE project comes in (Development of Sodium Ion Technology for Industrially Scalable Energy Storage).
Improving Storage Capacity and Cycle Stability
ENTISE focuses on the further development of existing material concepts and processes. Technologically, the storage capacity of the cathode and anode in particular is to be improved, for which the materials used, including the electrolytes used, must be optimized. In addition, the cycle stability, i.e. the ability of the cells to ensure stable performance even after repeated charging and discharging, is to be improved through the development of new materials, optimized electrode materials and coatings.
In the final phase of the project, the individual components will be scaled up and transferred from the laboratory to pre-industrial scale (piloting) in cooperation between the industrial and research partners. At the end of the project, a small series of round cells will be produced, which will enable a reliable assessment of properties in practical application scenarios such as stationary storage systems. An accompanying technical, economic and ecological evaluation will round off the project. A central component is then the production of sufficient quantities to build individual resilient laboratory samples through to prototypes in round cell design.
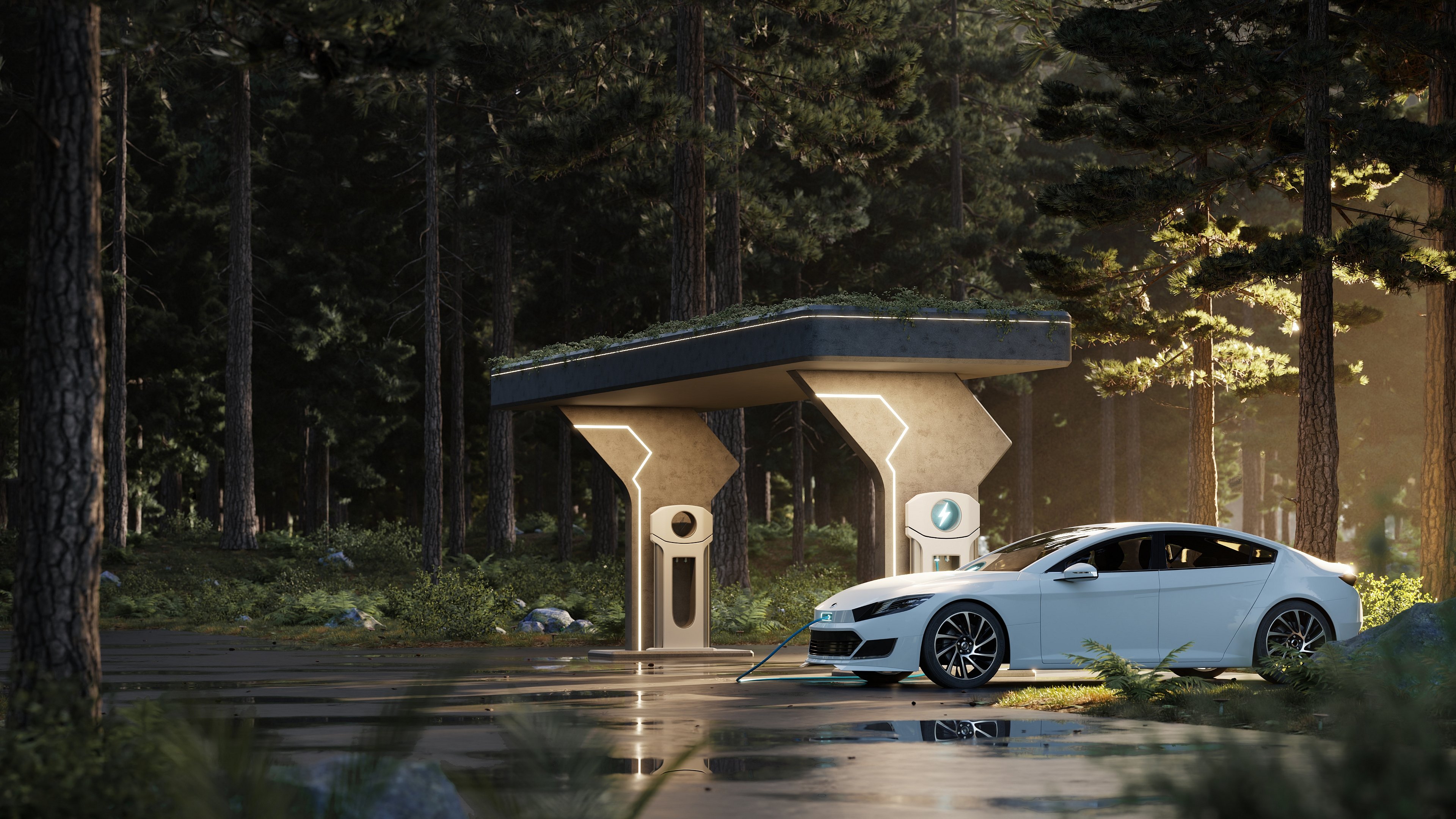
From Prototypes to Market-Ready Cells for Electric Vehicles or Home Storage Systems
Together with the project partners, our R&D team will define and research suitable material systems for use as cathode materials and make them available for application tests. We are developing solutions for scaling up the process, which will be investigated within the project network. VARTA Microbattery GmbH (initiator and project coordinator) is responsible for the evaluation of materials available on the market, as well as for the production of reference and prototype cells. VARTA Storage GmbH is responsible for cell benchmarking, as well as use-case testing for stationary storage applications.
Further project partners are the Helmholtz Institute Ulm; the Humboldt University of Berlin; the University of Freiburg (Freiburg Materials Research Center); the Center for Solar Energy and Hydrogen Research Baden-Württemberg; the Justus Liebig University Giessen; the Karlsruhe Institute of Technology (Institute for Nanotechnology, Battery and Electrochemistry Laboratory); the Research Center Jülich; EurA AG; E-Lyte Innovations GmbH and the Karlsruhe Institute of Technology (Institute for Applied Materials – Energy Storage Systems).
Development Process for a Sodium-Ion Battery
Suitable layered oxides are defined as active materials and then scaled up. Within the project we try to generate Na-ion active materials with the required target specifications (morphology and composition) and to develop a suitable manufacturing process with the aid of the pulsation reactor. The generated samples will be made available to the partners for application tests. Based on these application tests, the active material systems are to be systematically researched, further developed and scaled up at our company. Together with our parent company IBU-tec, we are involved in the development and production of the cathode active material in a combination of process steps in pulsation reactors and thermal post-treatment in a rotary kiln.
In the initial stages of the project, performance parameters were defined and a specific sodium manganese oxide cathode active material was selected – optionally with or without additives. If the results are satisfactory and performance is good enough, a scale-up for the production of the active cathode material will follow, while retaining the properties achieved in the pilot plants. Subsequently, the energy optimization of the process takes place in order to reduce possible production costs.