BiSSFest – Development of a Solid-State Battery
Solid-State Battery as a Further Development of the Lithium-Ion Battery
Nowadays, lithium-ion batteries are an integral part of everyday life. They are used in cell phones, notebooks and e-bikes. However, the demands on accumulators and batteries continue to rise, and research into new types of battery systems is becoming increasingly important. The solid-state battery offers the next step towards higher energy density and greater safety at the same time!
Principle of a Solid-State Battery
As the name suggests, the liquid electrolyte previously used in solid state batteries is now replaced by a solid Li-ion conductor. The elimination of the mostly organic electrolyte reduces the flammability of the entire battery. The sulphide-based material class has proven to be particularly promising. These have a high Li-ion conductivity with good mechanical processability.
Project Description
The research project “Bipolar Stacking of Sulfide Solid State Batteries” – BiSSFest for short – aims to develop scalable technologies along the value chain, while at the same time evaluating scalability from laboratory to production scale. The use of a solid electrolyte also allows bipolar stacking of the electrodes, in which the individual cells are stacked directly on top of each other and connected in series. “Bipolar” refers to the electrode structure, in which the electrode carriers are both the active materials for the cathode of the battery and the active materials for the anode on the back. This structure increases the cell voltage and contributes to material savings through reduced contacting of the current arresters, so that the energy density can be further increased.
BiSSFest Project Partners
The project consortium consists of eight partners along the entire battery production value chain. The Fraunhofer Institute for Surface Engineering and Thin Films (IST) covers the synthesis of sulfidic solid-state electrolytes, including Li6PS5Cl, which is to be produced by mechanochemical synthesis as part of the project. Netzsch-Feinmaltechnik GmbH is developing a scalable mill for this in which the synthesis takes place on a kg scale. We at IBUvolt then coat the cathode active materials lithium nickel manganese cobalt oxides with specially developed inert oxides, which stabilize the material. The resulting composite materials are then tested for their electrochemical performance by the Wilhelms University of Münster.
The lithium metal anodes are produced in two versions (separator side and current collector side) at the Fraunhofer Institute for Surface Engineering and Thin Films. Electrodes for solid-state batteries are manufactured from the composite materials by the Institute for Particle Technology at the Technical University of Braunschweig and the cell production for the bipolar stacking takes place at the Institute for Machine Tools and Production Technology. The new cells developed in this way will then be tested with the expertise of EL-CELL GmbH. Finally, Custom Cells Itzehoe GmbH is implementing the scalable production.
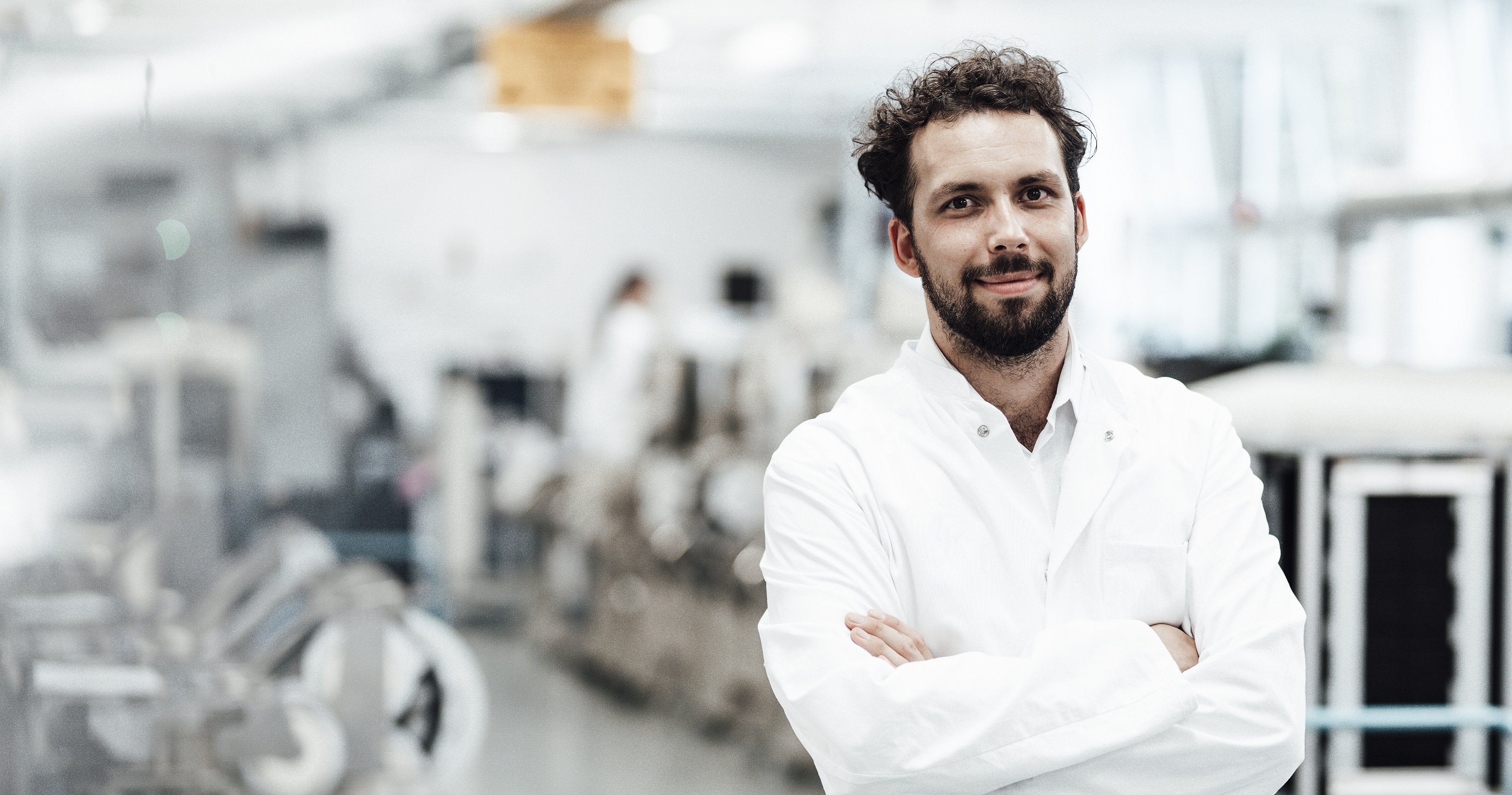
Current Project Status and Further Goals
The use of a solid-state electrolyte also increases the demands on the cathode active material. Lithium nickel manganese cobalt oxides, currently used in liquid batteries, must first be additionally stabilized. Stabilization is achieved by coating with various inert oxides to prevent the active material from reacting with the solid electrolyte. This is where our expertise comes into play! Thanks to our portfolio of nanoscale oxides, we have access to a wide range of suitable coating materials. Decades of experience in thermal process engineering and a number of pilot plants of various sizes give us the opportunity to develop a continuous coating process.
Cathode Material Coating
Various approaches were considered for the coating itself. Coatings were applied on a laboratory scale using the Pechini process. This is a process for producing solid (non)metallic inorganic or hybrid polymer materials from colloidal dispersions. Powders, coatings or aerogels can be produced by further processing the brines.
In order to ensure scalability and to establish a continuous process, further tests were carried out on our native pulsation reactors, in which the preparation was carried out using solids or aqueous suspensions. To ensure comparability, the coating was carried out in an intensive mixer.
The composite materials thus obtained were sent to the project partners, where they were tested for their suitability for battery systems. The project partners have already been able to use them to produce solid-state batteries and test their performance. It was also possible to generate bipolar stacked battery cells. Until the end of the project, research will continue on the cycle stability and capacity of both systems through suitable material optimization.